Die Casting Mould Factory: Excellence in Metal Fabrication
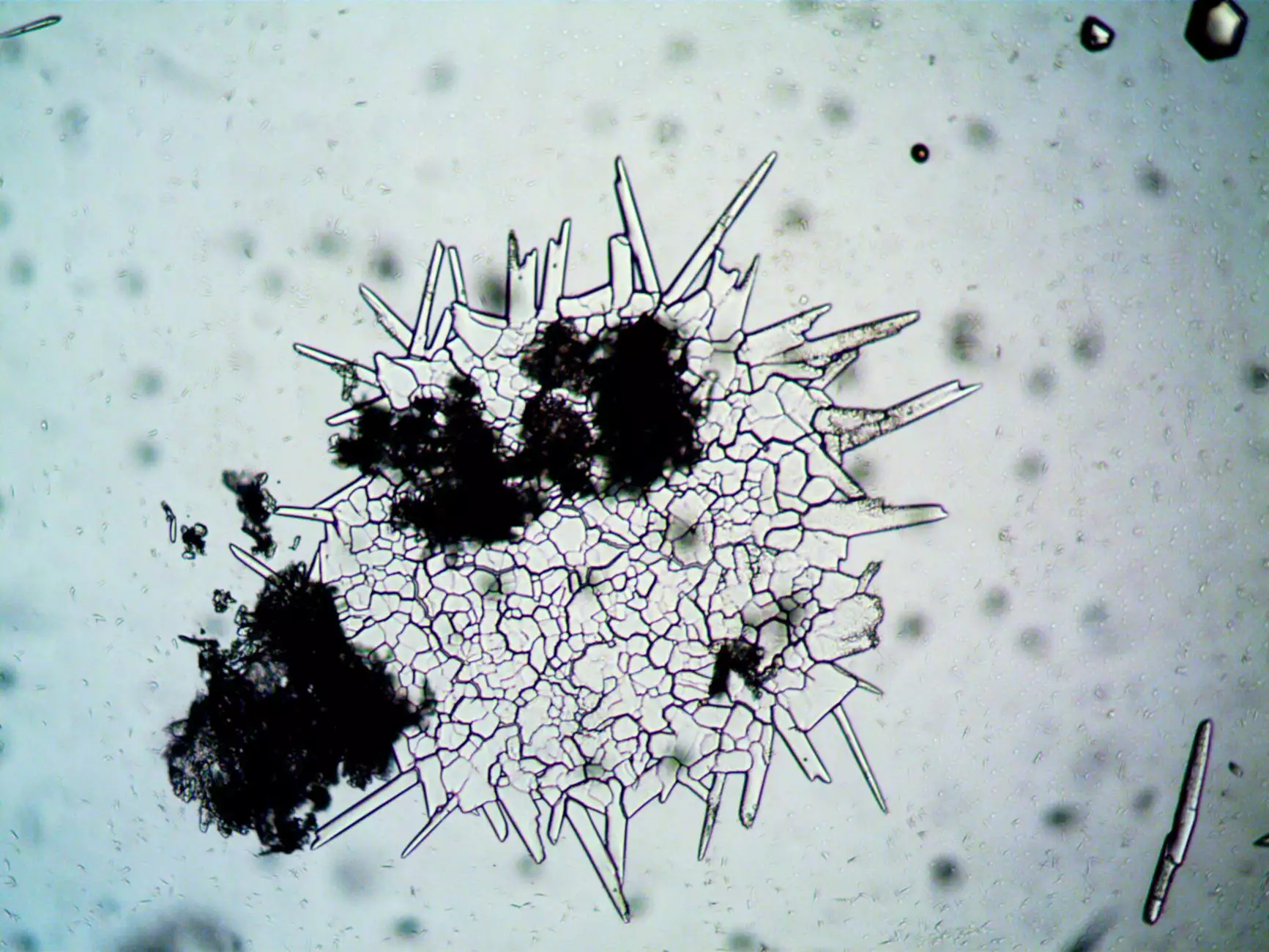
In an era where precision and efficiency drive manufacturing, the die casting mould factory stands at the forefront of innovation in the metal fabrication industry. This article delves deep into the workings, advantages, and future of die casting moulds, showcasing why this manufacturing process is essential for modern industries.
The Fundamentals of Die Casting
At its core, die casting is a metal casting process that involves forcing molten metal into a mold cavity. The process is characterized by:
- High Pressure: The molten metal is injected into the mold under high pressure, ensuring precision and reducing waste.
- Reusability: The molds created in a die casting mould factory are designed for repeated use, making them cost-effective over time.
- Material Options: Die casting is commonly used with metals such as aluminum, zinc, and magnesium.
Advantages of Using Die Casting Moulds
Choosing die casting moulds for your manufacturing needs comes with a plethora of advantages:
1. Precision and Accuracy
The high-pressure injection of molten metal into a mold results in parts that have exceptional precision. This level of accuracy is critical in industries such as automotive and aerospace where tight tolerances are mandatory.
2. Complex Geometries
Die casting allows for the production of complex shapes that would be impossible or economically unfeasible with other manufacturing processes. This capability opens the door for innovative product designs.
3. Cost-Efficiency
While the initial investment in a die casting mould factory can be significant, the long-term savings due to reduced material waste and increased production rates are substantial. The reusable nature of the moulds further contributes to a lower cost per unit.
4. Superior Surface Finish
Parts produced through die casting often require minimal post-processing due to their excellent surface finish, which can reduce labor and enhance the product's aesthetic appeal.
5. High Production Rates
Die casting mould factories can produce thousands of parts per hour, which is essential for meeting the demands of large-scale production.
Industries Utilizing Die Casting
The versatility of die casting means that it is employed in a wide range of sectors. Notable industries include:1. Automotive Industry
The automotive sector regularly utilizes die casting to manufacture components such as engine blocks, transmission housings, and various structural parts. These components benefit from the strength and lightweight characteristics of die cast materials.
2. Aerospace Industry
In aerospace, precision is paramount. Die casting mould factories supply parts that meet stringent safety and performance standards, ensuring the reliability of aircraft components.
3. Consumer Electronics
The consumer electronics market often requires intricate designs in lightweight materials, which makes die casting an ideal choice for parts like housings and connectors.
4. Industrial Machinery
Manufacturers of industrial machinery rely on die casting for durable and robust components, which are fundamental for performance and longevity.
The Process of Die Casting in a Die Casting Mould Factory
Understanding the die casting process is crucial for appreciating the expertise within a die casting mould factory. Here’s a step-by-step breakdown:
1. Design and Prototype
The first step involves designing the part to be manufactured. Engineers create detailed CAD models, which are then prototyped using 3D printing or other methods to test fit and design.
2. Mold Creation
Once the design is finalized, specialized engineers create the molds, typically from high-quality tool steel. The mold's design includes considerations for cooling channels and ejection mechanisms, crucial for effective production.
3. Melting the Metal
Metal is melted in furnaces and then transferred to the die casting machine. Temperature control is vital to ensure the metal is molten and flows well into the mold.
4. Injection
The molten metal is injected into the mold under high pressure. This phase is where the precision of die casting comes into play, as the metal must fill every nook and cranny of the mold to achieve the desired part shape.
5. Cooling
Following injection, the metal needs time to cool and solidify within the mold. Advanced cooling techniques are utilized to optimize this time, allowing for quick turnaround without sacrificing quality.
6. Ejection
Once the part has cooled, the mold opens, and the finished part is ejected. Any excess material, known as flash, is removed during this stage.
7. Finishing
Although die cast parts typically have a good surface finish, some may require additional machining, polishing, or coating to meet specific standards or customer requirements.
Future Trends in Die Casting
The die casting industry is continually evolving, and staying ahead means keeping an eye on emerging trends:1. Automation and Smart Manufacturing
As technology advances, die casting mould factories are increasingly integrating automation and IoT capabilities, which lead to improved manufacturing efficiency and the ability to monitor production in real-time.
2. Environmentally Friendly Practices
The industry's focus on sustainable practices is growing. Eco-friendly die casting techniques, such as the use of recycled materials, are becoming more popular.
3. Advancements in Materials
Research into new alloys and materials for die casting is ongoing, leading to the potential for even lighter, stronger, and more durable parts suitable for diverse applications.
Conclusion
In summary, a die casting mould factory is not just a manufacturing entity; it represents a powerful intersection of technology, creativity, and industrial expertise. Businesses across various sectors rely on the precision and efficiency of die casting to deliver high-quality products. As the industry evolves, embracing advances in automation and sustainable practices, we can expect die casting to remain a critical component of modern manufacturing.
For businesses looking to enhance their production capabilities with die casting, collaborating with a reputable die casting mould factory like DeepMould.net can lead to exceptional outcomes and competitive advantages in the market.